The Science Behind Porosity: A Comprehensive Guide for Welders and Fabricators
Comprehending the elaborate mechanisms behind porosity in welding is crucial for welders and makers aiming for remarkable workmanship. From the structure of the base materials to the intricacies of the welding procedure itself, a wide range of variables conspire to either exacerbate or relieve the existence of porosity.
Understanding Porosity in Welding
FIRST SENTENCE:
Evaluation of porosity in welding discloses important understandings into the integrity and high quality of the weld joint. Porosity, identified by the presence of cavities or spaces within the weld metal, is a typical concern in welding processes. These voids, otherwise correctly attended to, can jeopardize the architectural integrity and mechanical properties of the weld, resulting in prospective failings in the ended up item.
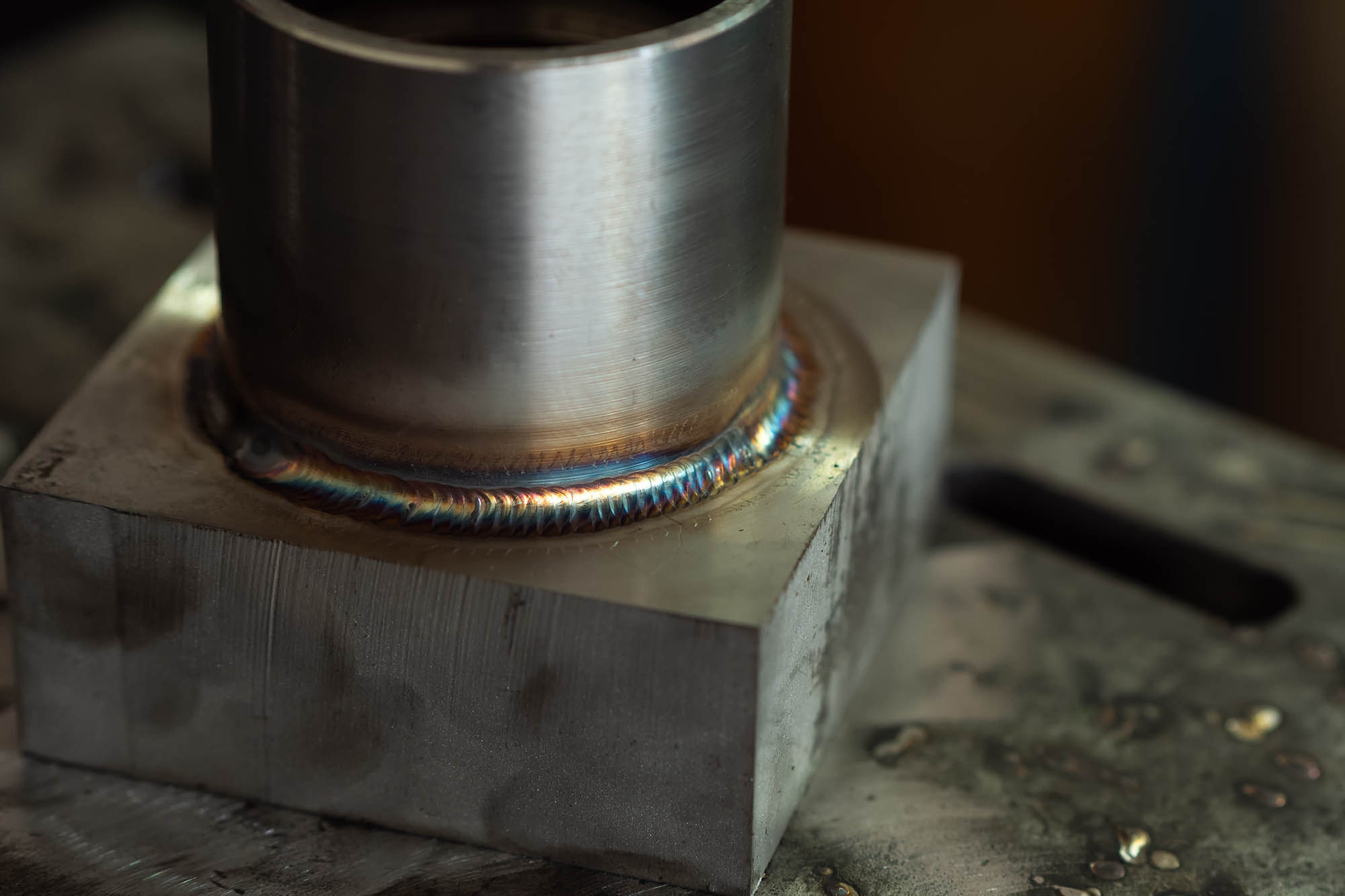
To spot and quantify porosity, non-destructive testing approaches such as ultrasonic screening or X-ray examination are usually utilized. These methods enable the identification of inner issues without jeopardizing the stability of the weld. By evaluating the size, form, and circulation of porosity within a weld, welders can make educated decisions to boost their welding procedures and accomplish sounder weld joints.
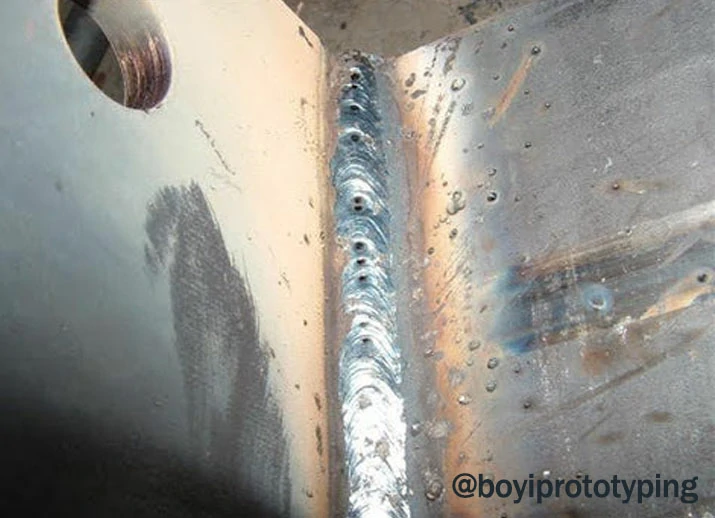
Aspects Influencing Porosity Development
The incident of porosity in welding is influenced by a myriad of aspects, ranging from gas securing efficiency to the details of welding specification settings. One vital element adding to porosity formation is poor gas shielding. When the protecting gas, generally argon or carbon dioxide, is not effectively covering the weld swimming pool, atmospheric gases like oxygen and nitrogen can pollute the liquified metal, causing porosity. Additionally, the tidiness of the base products plays a substantial function. Contaminants such as rust, oil, or dampness can evaporate during welding, producing gas pockets within the weld. Welding criteria, including voltage, present, take a trip rate, and electrode type, likewise effect porosity development. Using incorrect setups can produce extreme spatter or warm input, which subsequently can result in porosity. The welding technique employed, such as gas metal arc welding (GMAW) or shielded metal arc welding (SMAW), can influence porosity formation due to variations in warm distribution and gas protection. Comprehending and regulating these elements are necessary for decreasing porosity in welding procedures.
Results of Porosity on Weld Top Quality
The presence of porosity also deteriorates the weld's resistance to deterioration, as the trapped air or gases within the voids can react with the surrounding atmosphere, leading to destruction over time. In addition, porosity can hinder the weld's ability to endure stress or influence, more threatening the overall quality and reliability of the welded structure. In vital directory applications such as aerospace, vehicle, or architectural building and constructions, where safety and security and resilience are critical, the damaging results of porosity on weld top quality can have extreme effects, highlighting the value of lessening porosity with appropriate welding methods and procedures.
Techniques to Minimize Porosity
In addition, utilizing the ideal welding specifications, such as the proper voltage, present, and take a trip speed, is vital in avoiding porosity. Preserving a consistent arc length and angle throughout welding also helps decrease the chance of porosity.

Making use of the ideal welding strategy, such as back-stepping or her response using a weaving movement, can likewise help distribute warmth equally and lower the possibilities of porosity formation. By executing these techniques, welders can effectively minimize porosity and generate top notch bonded joints.
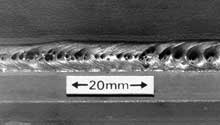
Advanced Solutions for Porosity Control
Implementing innovative innovations and innovative methods plays a pivotal function in accomplishing exceptional control over porosity in welding procedures. Additionally, using sophisticated welding methods such as pulsed MIG welding or customized ambience welding can also aid mitigate porosity concerns.
Another sophisticated remedy entails the use of sophisticated welding equipment. For example, using equipment with integrated functions like waveform control and innovative source of power can improve weld quality and minimize porosity risks. The implementation of automated welding systems with exact control over criteria can considerably lessen porosity problems.
Additionally, integrating advanced monitoring and inspection innovations such as real-time X-ray imaging or automated ultrasonic testing can aid in discovering porosity early in the welding procedure, enabling for instant corrective activities. In general, incorporating these innovative options can significantly improve porosity control and boost the general read the full info here quality of bonded elements.
Verdict
In final thought, understanding the scientific research behind porosity in welding is necessary for welders and fabricators to generate top notch welds. By determining the variables influencing porosity development and carrying out methods to decrease it, welders can boost the total weld quality. Advanced remedies for porosity control can even more enhance the welding procedure and make sure a solid and dependable weld. It is very important for welders to constantly educate themselves on porosity and carry out ideal methods to attain optimum results.