Porosity in Welding: Identifying Common Issues and Implementing Finest Practices for Prevention
Porosity in welding is a prevalent issue that typically goes unnoticed till it causes significant problems with the stability of welds. In this conversation, we will certainly check out the crucial factors contributing to porosity formation, examine its detrimental impacts on weld performance, and talk about the finest techniques that can be taken on to minimize porosity incident in welding processes.
Typical Reasons For Porosity
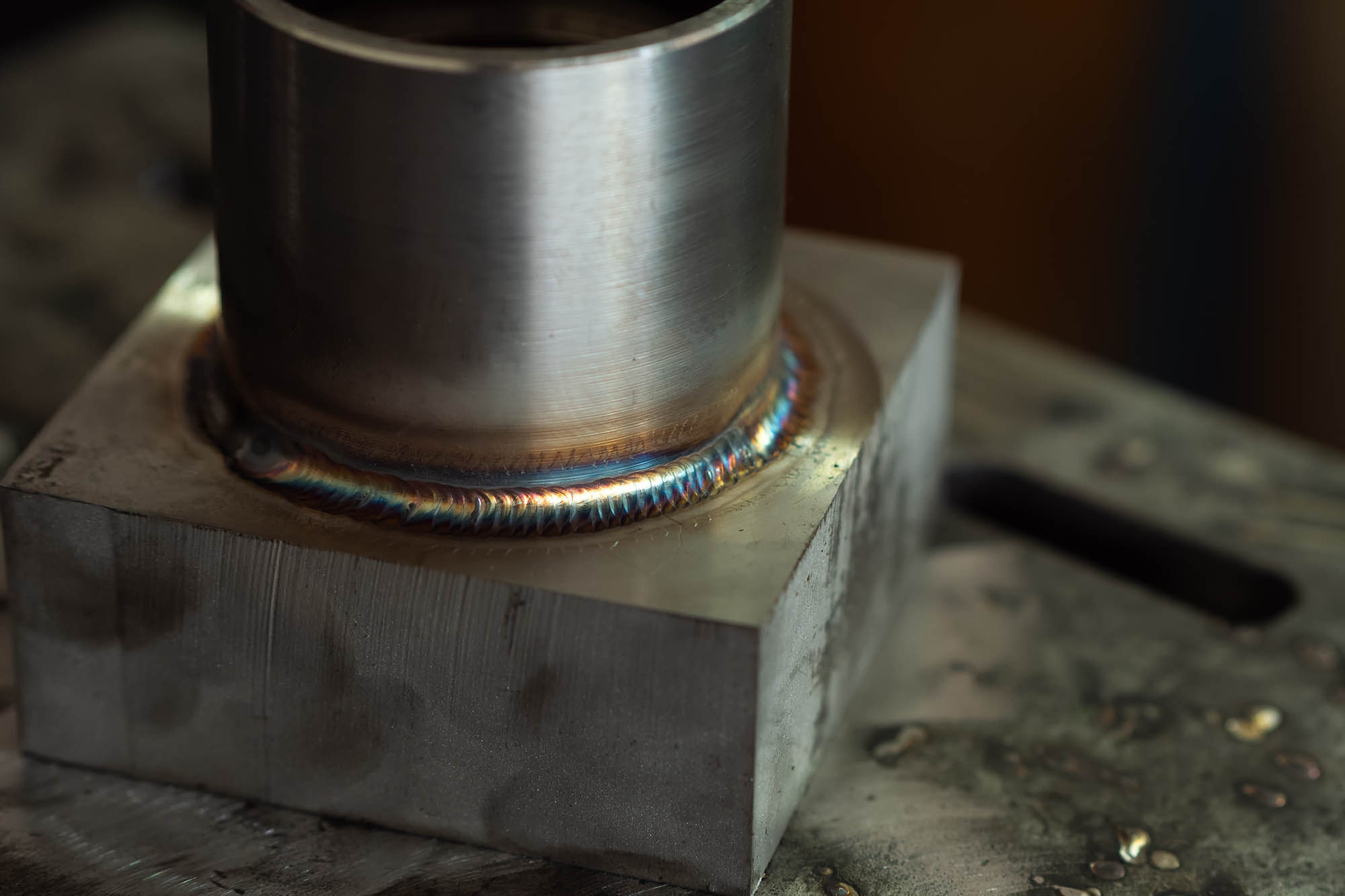
Utilizing dirty or damp filler materials can present contaminations into the weld, adding to porosity issues. To mitigate these usual causes of porosity, thorough cleaning of base steels, appropriate shielding gas selection, and adherence to optimal welding criteria are important techniques in accomplishing high-quality, porosity-free welds.
Influence of Porosity on Weld High Quality

The existence of porosity in welding can considerably jeopardize the structural stability and mechanical properties of welded joints. Porosity produces gaps within the weld metal, damaging its overall stamina and load-bearing ability. These voids act as anxiety concentration points, making the weld extra susceptible to fracturing and failure under applied lots. Additionally, porosity can minimize the weld's resistance to corrosion and various other ecological aspects, better lessening its durability and performance.
Welds with high porosity degrees often tend to display lower impact toughness and lowered capability to warp plastically before fracturing. Porosity can impede the weld's ability to effectively transmit forces, leading to premature weld failure and possible security dangers in essential frameworks.
Best Practices for Porosity Prevention
To enhance the architectural stability and top quality of bonded joints, what details steps can be executed to minimize the incident of porosity during the welding procedure? Making use of the proper welding method for the details material being bonded, such as adjusting the welding angle and gun placement, can even more this article protect against porosity. Regular examination of welds and prompt remediation of any type of concerns recognized during the welding procedure are necessary methods to avoid porosity and produce top notch welds.
Significance of Appropriate Welding Methods
Executing proper welding techniques is paramount in making sure the architectural stability and quality of welded joints, constructing upon the structure of effective porosity avoidance actions. Too much warm can lead to enhanced porosity due to the entrapment of gases in the weld pool. Furthermore, making use of the appropriate welding parameters, such as voltage, current, and take a trip speed, look at this web-site is essential for attaining sound welds with very little porosity.
In addition, the selection of welding process, whether it be MIG, TIG, or stick welding, ought to line up with the certain needs of the task to make certain optimal results. Proper cleaning and preparation of the base metal, along with choosing the ideal filler product, are also vital parts of skilled welding techniques. By sticking to these best practices, welders can decrease the danger of porosity formation my link and produce top quality, structurally audio welds.
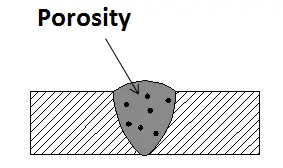
Checking and Quality Assurance Procedures
Evaluating procedures are essential to detect and prevent porosity in welding, making certain the toughness and resilience of the final item. Non-destructive screening methods such as ultrasonic screening, radiographic screening, and visual assessment are commonly utilized to identify potential issues like porosity.
Post-weld assessments, on the other hand, examine the last weld for any problems, including porosity, and validate that it satisfies specified requirements. Carrying out a thorough quality control plan that consists of complete testing treatments and assessments is paramount to lowering porosity concerns and ensuring the overall top quality of bonded joints.
Final Thought
In verdict, porosity in welding can be a common concern that influences the top quality of welds. By determining the common reasons of porosity and implementing finest techniques for avoidance, such as appropriate welding strategies and testing actions, welders can make sure high quality and trustworthy welds. It is vital to focus on avoidance approaches to decrease the event of porosity and keep the stability of welded frameworks.